Druppelafscheiders
Vane-type afscheiders
Vane-type afscheiders bestaan doorgaans uit parallelle profielen die de efficiëntie van de afscheider bepalen op basis van hun vorm en lengte in de stroomrichting. Een meer gebogen en complex profiel maakt het mogelijk kleinere druppels te scheiden, aangezien hun massa-inertie ervoor zorgt dat ze worden afgescheiden van een rechter en eenvoudiger profiel. Wanneer een fijner druppelspectrum nodig is voor het scheiden van vloeistofdruppels uit gasstromen, worden vane-type afscheiders vaak gebruikt voor zowel verticale als horizontale gasstromen. Wanneer er een risico op vuilafzetting is, kunnen de afscheiders discontinu of continu worden doorgespoeld. In extreme gevallen kan een meertraps systeem noodzakelijk zijn, waarbij de eerste scheidingsfase bijzonder intensief wordt gespoeld. Vane-type afscheiders bereiken een hoge scheidingsgraad van 99,9%. Het belangrijkste verschil tussen verticaal en horizontaal stromende vane-type afscheiders ligt in de constructie; de lamellen van een verticaal type zijn horizontaal gekanteld of onder een kleine hoek ten opzichte van het horizontale vlak, en de vloeistof moet in de tegenovergestelde richting van het gas stromen. Het ontwerp van een verticaal stromend afscheiderprofiel moet zones met lage snelheid op de profielen omvatten, waar afgezette vloeistofdruppels zich kunnen ophopen zonder in aanraking te komen met de gasstroom erboven. Deze zones worden ook gebruikt voor het effectief verwijderen van de vloeistofdruppels uit de lamellenscheider. Een met druppels beladen gasstroom passeert een labyrint bestaande uit gebogen en geprofileerde lamellen. De vloeistofdruppels, die in de gasstroom terechtkomen, worden door hun massa-inertie van hun oorspronkelijke pad afgeleid binnen dit labyrint. De efficiëntie van dit scheidingsproces hangt af van factoren zoals de geometrie van de profielen, de eigenschappen van het gas en de vloeistof, de druppelgrootte en de druppellading. Als een druppel in contact komt met de profielwand van de lamellen, wordt het beschouwd als een grensdruppel en onder specifieke omstandigheden volledig gescheiden. Druppels met een diameter gelijk aan of groter dan deze grensdruppels worden ook volledig gescheiden. Echter, druppels kleiner dan de grensdruppels worden slechts gedeeltelijk gescheiden, resulterend in een fractionele scheidingsgraad. Deze graad kan worden gebruikt om de prestaties van het scheidingssysteem te evalueren. Dit onderdeel kan worden beschouwd als een fractionele scheidingsgraad.
Wire mesh demisters
Het principe achter de werking van een wire mesh demister, vergelijkbaar met een vane-type afscheider, berust op massa-inertie. Wanneer de grootte van de te scheiden vloeistofdruppels aanzienlijk kleiner is dan 10 micron, kan een wire mesh demister worden gebruikt. Deze demister is geconstrueerd met dunne draden die ingewikkeld geweven zijn tot een driedimensionale mat. De demistermat kan op maat worden gemaakt in verschillende vormen, waardoor deze kan worden toegepast in verticaal stromende systemen. Voor toepassingen met een kleinere diameter wordt vaak een enkelvoudige afscheider gebruikt, terwijl grotere oppervlakken meerdere onderdelen vereisen om verwijdering via een mangat mogelijk te maken. De efficiëntie van de demister wordt bepaald door de samenstelling van de mat, waarbij een dunne draadafstand ideaal is voor het scheiden van fijne druppels. Het reinigen van een wire mesh demister is uitdagend, waardoor het alleen geschikt is voor vloeistoffen die geen vuilafzetting veroorzaken. Daarom is het gebruik van een wire mesh demister vaak niet haalbaar in vuile toepassingen. Het is vrij gebruikelijk om scheidingsgraden van 99,9% te bereiken voor druppelgroottes variërend van 5 tot 20 micron met een wire mesh demister. Echter, in tegenstelling tot vane-type afscheiders voor verticale stroom, moeten aanzienlijke drukverliezen in overweging worden genomen, variërend van 1,5 tot 4 mbar. Deze verliezen zijn sterk afhankelijk van de vloeistofbelasting van het gas. Het is belangrijk op te merken dat wire mesh demisters alleen als fijne afscheiders kunnen worden gebruikt vanwege het risico op vuilafzetting en verstoppen van de verpakking. Tijdens het scheidingsproces passeren de druppels de filtermat, botsen ze op het draadoppervlak door massa-inertie, en agglomereren ze bij de draden voordat ze terugvallen als grotere druppels. De scheidingsprestaties worden beïnvloed door het vrije volume en het specifieke draadoppervlak van de mat, en verbeteren met toenemende gasstroomsnelheid. Het is echter cruciaal om de maximale snelheid niet te overschrijden om overstroming te voorkomen, wat verwijst naar het meeslepen van druppels. Voor een 99,9% fractionele scheidingsgraad ligt de grensdruppelgrootte doorgaans tussen de 5 en 10 micron voor standaardversies. Met speciale constructies en een passend ontwerp is het echter mogelijk om een dergelijke scheiding te bereiken voor druppels zo klein als 3 micron. Om de demistermatten te ondersteunen, worden meestal speciaal ontworpen ondersteunings- en/of dekroosters geleverd, die zodanig zijn ontworpen dat het vrije doorstroomoppervlak ongeveer 90% bedraagt. Bij het installeren van de wire mesh demister moet erop worden gelet dat de demistermat nauw aansluit op de kolomwand zodat er geen valse lucht kan ontsnappen. De mathoogte van de wire mesh demister is 100 tot 150 mm voor de meeste toepassingen. Als de gasstroom zeer fijne druppels bevat, zoals die veroorzaakt door condensatie, kan een aanzienlijk grotere mathoogte of een meerlagige structuur nodig zijn.
Open spray systemen
Dit type wasinstallatie werkt met een gesloten kringloopsysteem, waarbij de wasvloeistof wordt rondgepompt vanuit het geïntegreerde buffer. Om een langdurig sproeiproces te garanderen, is het scrubbersysteem uitgerust met meerdere volledig verwijderbare sproeilansen, gerangschikt in lagen. Deze sproeilansen bestaan uit sproeiers, waarvan sommige co-current en andere counter current zijn gemonteerd. De precieze positionering van deze sproeiers binnen de scrubber is cruciaal voor een effectieve gasbehandeling, omdat het zorgt voor grondig contact tussen de wasvloeistof en het procesgas, waardoor deeltjes worden vastgelegd. De tangentiële sproeiers, die zijn ontworpen om verstopping te voorkomen, produceren fijne druppels met een uniform sproeipatroon om de opvang van stof- en gasdeeltjes te maximaliseren. Door optimale absorptie kan een significante vermindering van verontreinigende deeltjes en gassen worden bereikt. Het ontwerp van het scrubbersysteem zorgt ervoor dat de sproeiers, met hun hoge gecombineerde debiet, tegelijkertijd het interieur van het wasgedeelte reinigen. Het overlappende sproeipatroon dat wordt gecreëerd door de positionering van de sproeiers resulteert in een uiterst efficiënt reinigingssysteem. Dit betekent dat de vervuilde gassen de sproeisectie niet kunnen passeren zonder te worden geabsorbeerd. Hierdoor is er geen pakking nodig, wat de drukval verhoogt, wat resulteert in een uitzonderlijk lage en consistente drukval. Dit type scrubber is bijzonder geschikt voor het afhandelen van onregelmatige concentraties of piekafvoeren, terwijl de vloeistof-naar-gasverhouding niet zo gevoelig is als bij gepakte bed scrubbers.
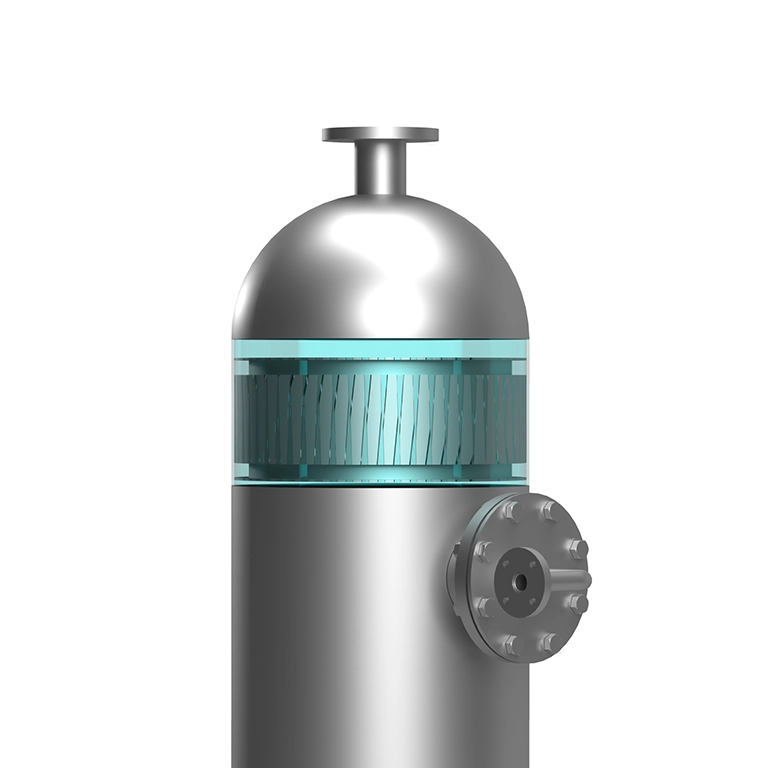
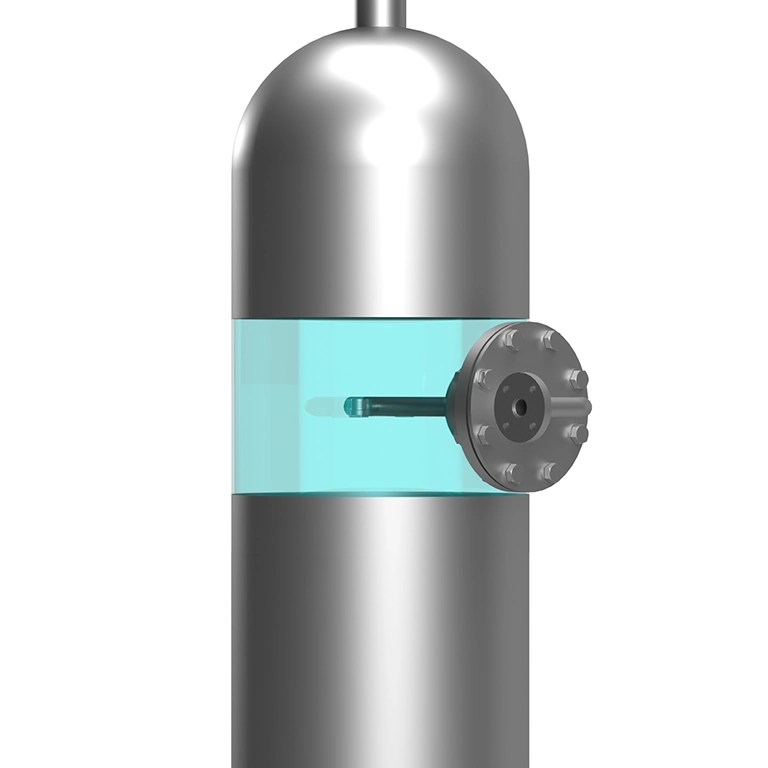
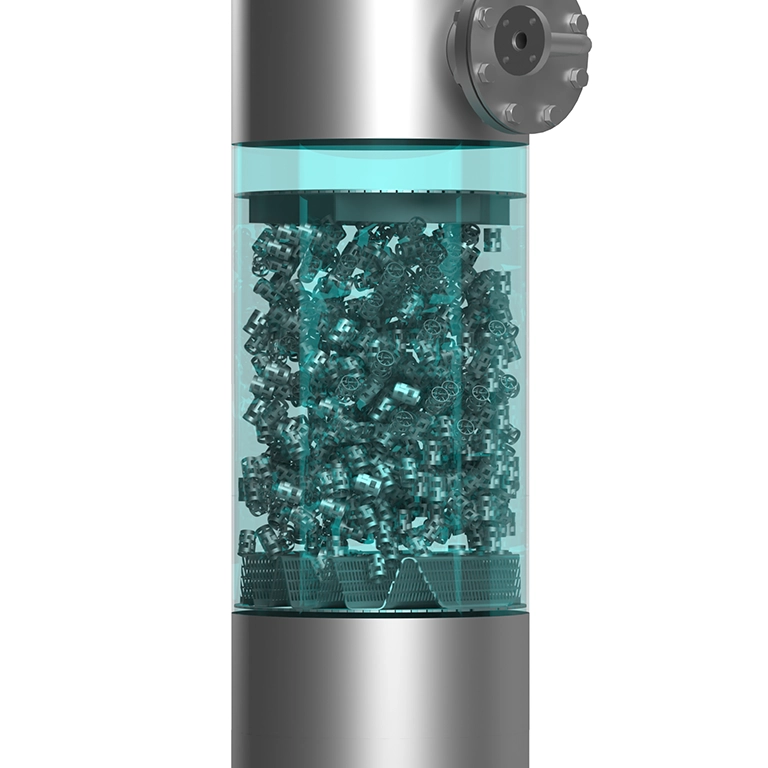
Holle conus sproeiers
Dit type sproeier is erg populair vanwege een zeer belangrijke eigenschap: druppelgrootte. Holle conussen produceren fijnere druppels dan enig ander type hydraulische (éénfase) sproeiers. Het grootste voordeel van fijne druppels is dat het oppervlak van alle opgehoopte druppels enorm is in verhouding tot de andere genoemde typen. Er zijn twee typen holle conus sproeiers: axiale en tangentiële inlaat. De inkomende vloeistofstroom in axiale sproeiers staat in lijn met de aansluiting waar de vloeistof in de sproeier in rotatie wordt gebracht door een specifiek wervellichaam. Deze draaiende vloeistofst room wordt vervolgens via een sproeieropening in de omgeving gesproeid, waardoor de vorm van een holle conus ontstaat. Tangentiële holle conus sproeiers zijn veel eenvoudiger van constructie dan axiale sproeiers. Een tangentiële inkomende vloeistofstroom brengt deze in rotatie, waarbij de cilindrische binnenkant van de sproeier wordt voorzien van een vloeistoffilm die de grootte van de druppel beïnvloedt. Wanneer de vloeistoffilm via de sproeiopening uit de sproeier wordt afgevoerd, ontstaat een kegelvormig sproeipatroon. Excentrische holle conus sproeiers zijn veel minder vatbaar voor verstopping dan axiale typen vanwege hun zijwaartse inlaat en dus het ontbreken van een wervellichaam. De holle conus sproeiers worden voornamelijk door Ravebo gebruikt in gaswassers en quenchers vanwege hun homogene sproeipatroon met fijne druppels.
Volledige conus sproeiers
Volledige conus sproeiers worden gebruikt voor een breed scala aan toepassingen. Deze sproeiers hebben ook een kegelvormig sproeipatroon, maar hier is de kegel gesloten. Dit betekent dat de volledige conus sproeier de eerste keuze is wanneer een gelijkmatige oppervlaktedekking of vloeistofverdeling vereist is. In tegenstelling tot holle conus sproeiers produceren volledige conus sproeiers een vrij grove druppel die een grotere kinetische energie heeft in vergelijking met holle conus sproeiers. Dit betekent dat de impact op het sproeioppervlak veel hoger is. Vanwege deze eigenschappen wordt dit type sproeier vaak gebruikt voor reinigingstoepassingen. Net als holle conus sproeiers zijn volledige conus sproeiers ontworpen als axiale en tangentiële sproeiers. Beide typen hebben een wervellichaam dat de draaiende stroom beïnvloedt. Zonder deze elementen zou de sproeier een soort holle conus-uiterlijk hebben. Volledige conus sproeiers worden voornamelijk gebruikt in scrubbers met een gepakt bed vanwege hun goede vloeistofverdeling en spreiding.
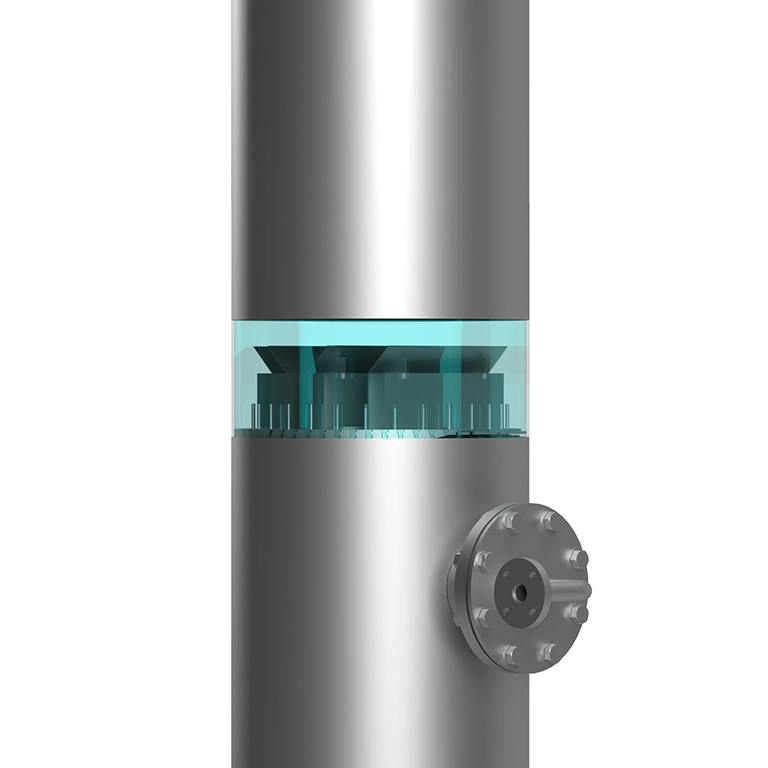
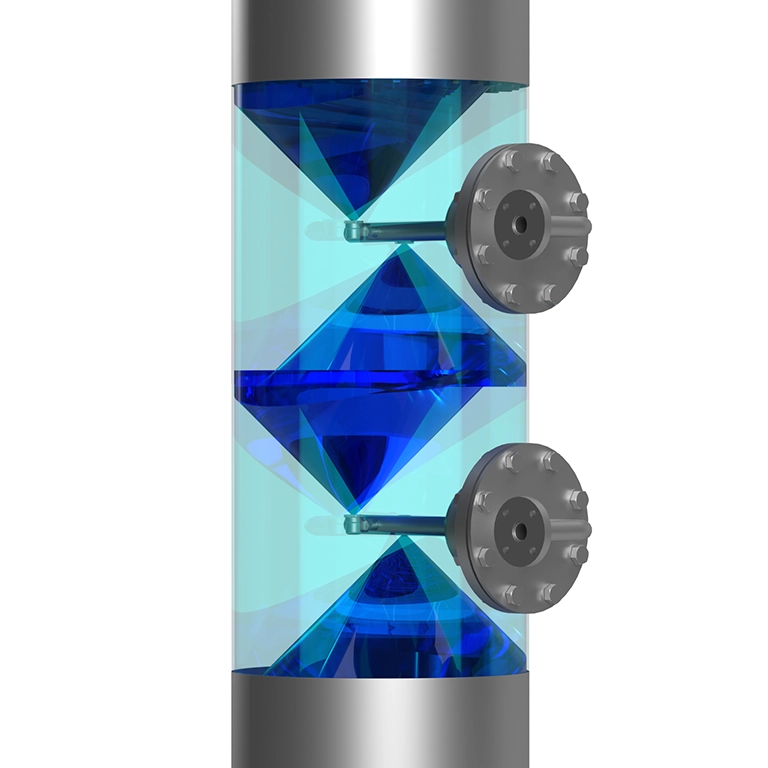
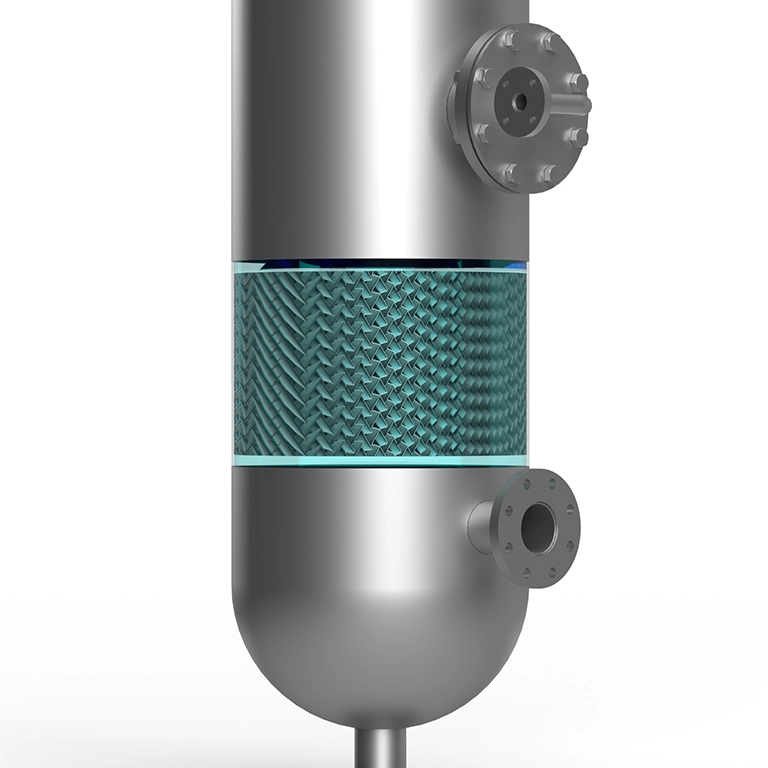
Gepakte bed scrubbers
Pakkingen voor absorptietorens
In dit type scrubber wordt een pakking gebruikt om een groot contactoppervlak te creëren tussen gas en vloeistof om een goede absorptie te verkrijgen. Aanvankelijk werd keramiek gebruikt als het belangrijkste materiaal voor willekeurige pakkingen in absorptietorens. Echter, hun gevoeligheid voor beschadiging, ongunstige volume-oppervlak verhouding, en hoge kosten hebben geleid tot een afname in hun gebruik. Als gevolg hiervan wordt de markt nu voornamelijk gedomineerd door metalen en kunststof pakkingen. Metalen pakkingen zijn over het algemeen ongeschikt voor corrosieve stoffen zoals zuur gas, terwijl kunststof pakkingen niet geschikt zijn voor toepassingen bij hoge temperaturen. Gepakte kolommen die het tegenstroomprincipe volgen, zijn het meest gebruikte type. Wanneer het afvalgas omhoog beweegt in de kolom, wordt weerstand gecreëerd door de pakkingen en de in tegengestelde richting stromende wasvloeistof. De drukval in de kolom hangt af van de gas- en vloeistofstromen, evenals het specifieke oppervlak en het vrije volume van de pakkingen. Een significante drukval vereist een krachtige ventilator om het gas door de kolom te duwen, wat resulteert in verhoogde kosten. Er zijn specifieke boven- en ondergrenzen voor de wasvloeistof- en gasstromen in elke kolom om optimale prestaties te garanderen. Als de gasstroomsnelheid te hoog wordt, kan dit de weerstand tegen de wasvloeistof zo verhogen dat de vloeistof niet langer vrij door de kolom kan stromen. Dit leidt tot de ophoping van de wasvloeistof, waardoor het hele gasoppervlak wordt geblokkeerd en de drukval toeneemt. Hierdoor kunnen de wasvloeistof en het gas niet effectief mengen. Wanneer alle beschikbare ruimte in de pakkingen is gevuld met wasvloeistof en deze begint op te stijgen in de kolom, wordt de scrubber als overstroomd beschouwd. De meeste gepakte kolommen werken op ongeveer 60 tot 70 procent van de gasoverstroom snelheid, aangezien het niet praktisch is om een kolom onder overstroomde omstandigheden te laten werken. Daarnaast is een minimale vloeistofstroomsnelheid noodzakelijk om de pakkingen adequaat te irrigeren en een efficiënte massatransfer tussen het gas en de wasvloeistof te faciliteren.
Vloeistofverdeler
Een vloeistofverdeler is specifiek ontworpen om een gelijkmatige verdeling van vloeistof over de pakkingen te waarborgen en een uniforme contact tussen de vloeistof- en gasfasen te faciliteren. Het is cruciaal dat de vloeistofverdeler de vloeistof gelijkmatig verdeelt, verstopping en verontreiniging voorkomt, voldoende ruimte biedt voor gasstroom, en operationele flexibiliteit mogelijk maakt. In hogere kolommen wordt vaak een vloeistofredistributieplaat gebruikt om vloeistof van de kolomwanden te verzamelen en naar het midden van de kolom te herverdelen. Deze herverdeling leidt tot verbeterd contact in het onderste gedeelte van de pakkingen. Over het algemeen zijn vloeistofredistributeurs vereist voor elke 2.500 tot 6.000 mm pakkinghoogte, afhankelijk van de kolomdiameter. Er zijn twee hoofdtypen vloeistofverdelers: zwaartekracht gebaseerde distributieplaten en druk gebaseerde systemen zoals sproeisystemen en geperforeerde pijpen. Sproeiers worden vaak gebruikt als distributiesystemen; echter, ze hebben de neiging om een fijne mist te produceren die gemakkelijk kan worden meegevoerd door de gasstroom. Bovendien zijn ze vatbaar voor verstopping en vereisen vaak hoge stromen om inadequate verdeling te compenseren. Aan de andere kant bestaan vloeistofverdelers meestal uit vlakke trays met meerdere goten voor gasstroom en perforaties in de traybodem voor vloeistofstroom. Het is opmerkelijk dat de trays zelf kunnen resulteren in een ongewenste drukval in de gasstroom.
Ondersteuningsplaten
Ondersteuningsplaten dienen het doel van het bieden van een stabiel platform voor pakkingmaterialen om op te rusten. In feite kunnen ondersteuningsplaten aanzienlijk grotere open oppervlaktes bieden dan de pakkingen zelf. Dit wordt bereikt door effectief gebruik te maken van ruimte in alle drie dimensies. Hierdoor kan deze functie effectief zorgen voor vermindering van drukval in processen met hoge stroomsnelheden. Daarnaast spelen afdekkingsplaten een cruciale rol bij het bevestigen van de pakkingmaterialen op hun plaats.
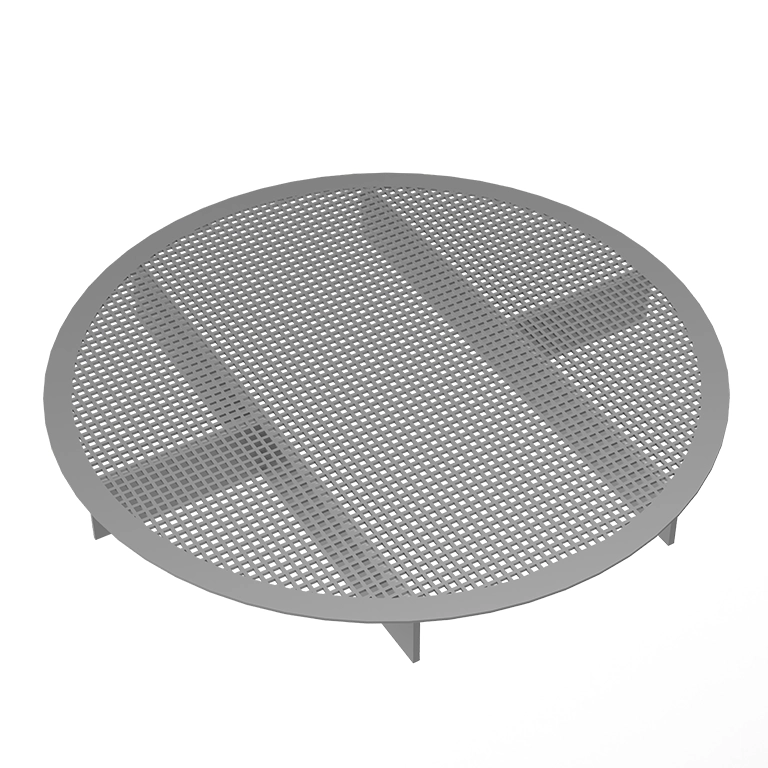
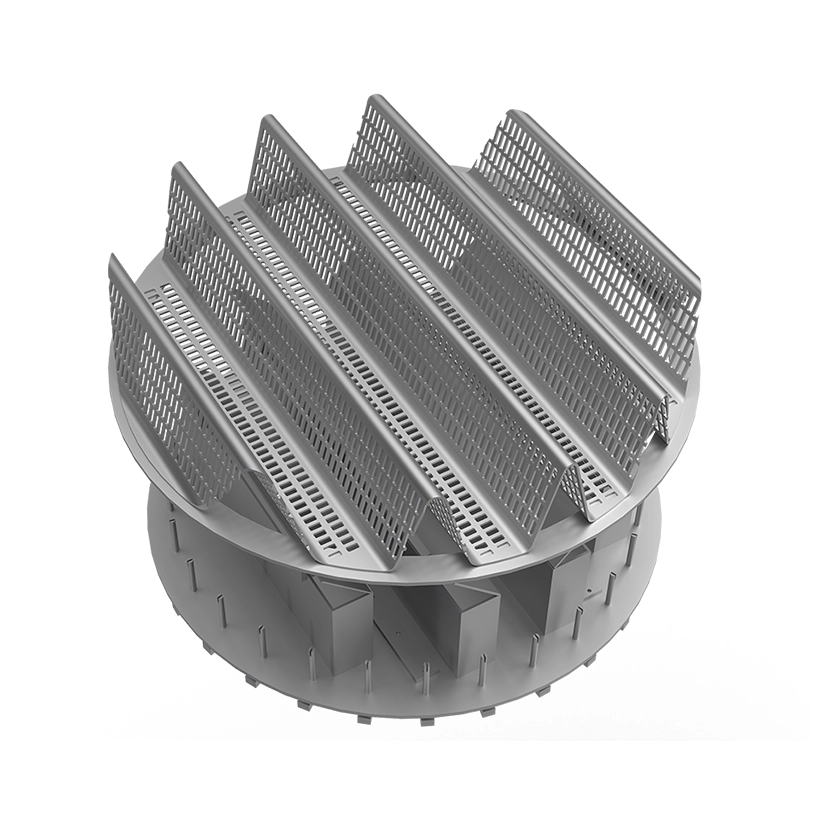
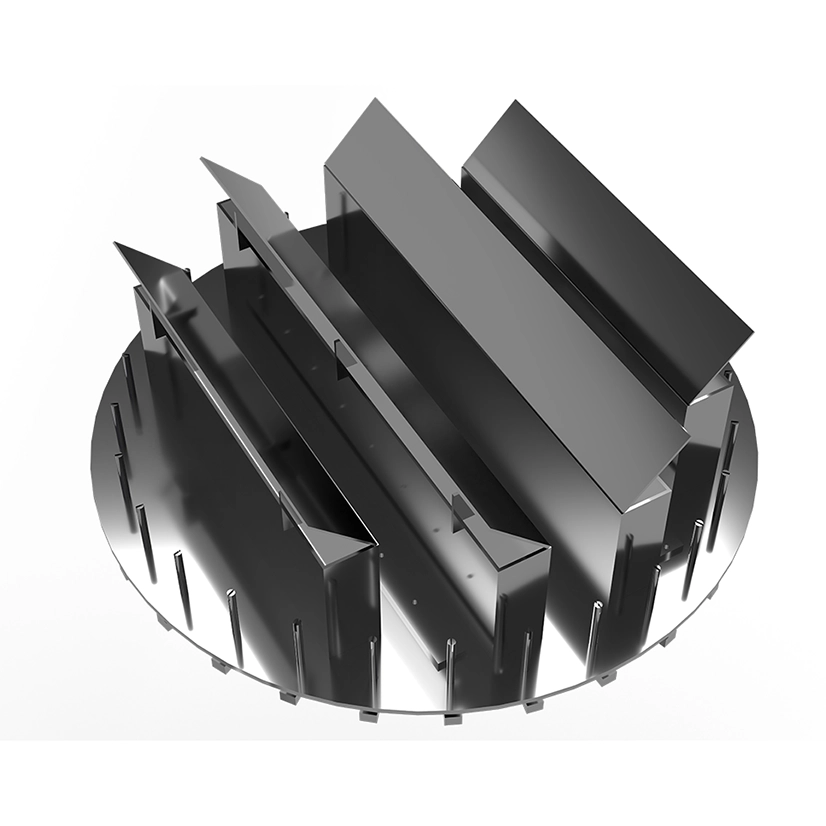
Afdekkingsplaten
Aan de andere kant spelen afdekkingsplaten een cruciale rol bij het vastzetten van de pakkingen op hun aangewezen positie. Het is mogelijk dat willekeurige pakkingen worden meegesleept in stroomafwaartse processen van de kolom als er geen afdekkingsplaat is gemonteerd. Hoewel dit geen frequent verschijnsel is, kan het niet worden uitgesloten en is het waargenomen in specifieke processen. Afdekkingsplaten houden de willekeurige pakkingen binnen de kolom door hun gewicht en weerstand tegen de verticale kracht die door de gasfase wordt uitgeoefend. Bedlimiters of afdekkingsplaten zijn apparaten die boven de willekeurige pakkingen worden gebruikt om fluidisatie te voorkomen, vooral tijdens verstoorde procesomstandigheden, en om de beweging van de pakkingen te beperken. Deze limiters zijn ontworpen om de interferentie met de vloeistofstroom te minimaliseren.